What Is Laser Marking Vision System?
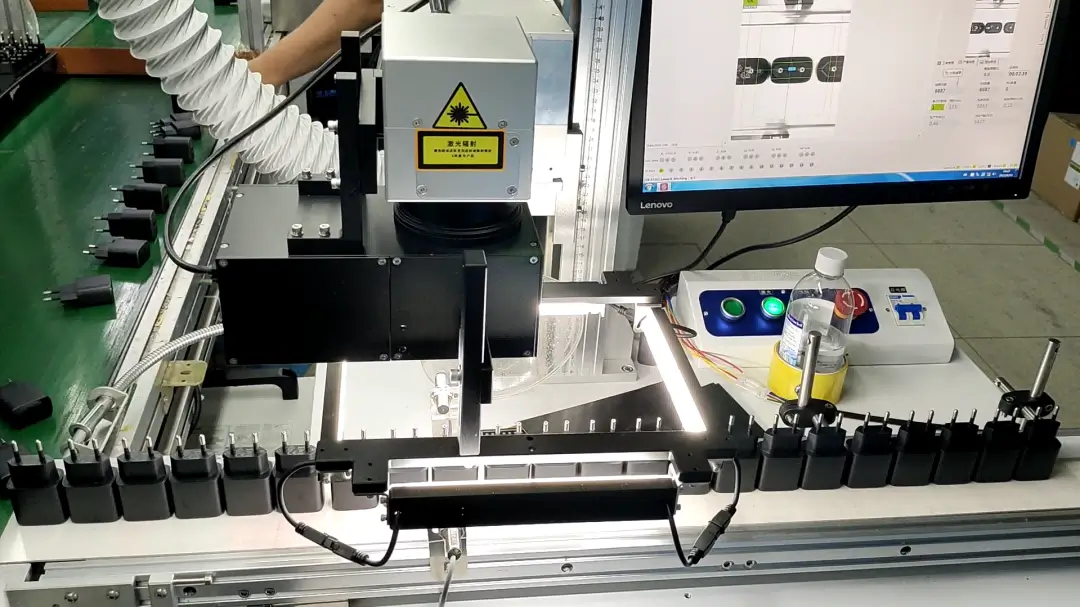
Why Vision System Is Needed in Laser Marking Process?
Problems we may encounter when laser marking bulk small parts manually:
- Slow and time-consuming: Manually positioning products with jigs can be slow and time-consuming, especially if you are working with small or complex parts (let’s say 100,000 small parts).
- High cost: If you have a lot of different types of products, you will need to create and maintain a lot of different fixtures. This can be expensive and time-consuming.
- Low efficiency: Manual marking can be inefficient, as you need to manually confirm the marking position for each product. This can lead to errors and decreased production capacity.
- High scrap rate: If the product is not placed correctly, it may be scrapped. This can lead to increased costs and decreased productivity.
- Low quality: Manual marking can sometimes be inaccurate, which can lead to quality problems.
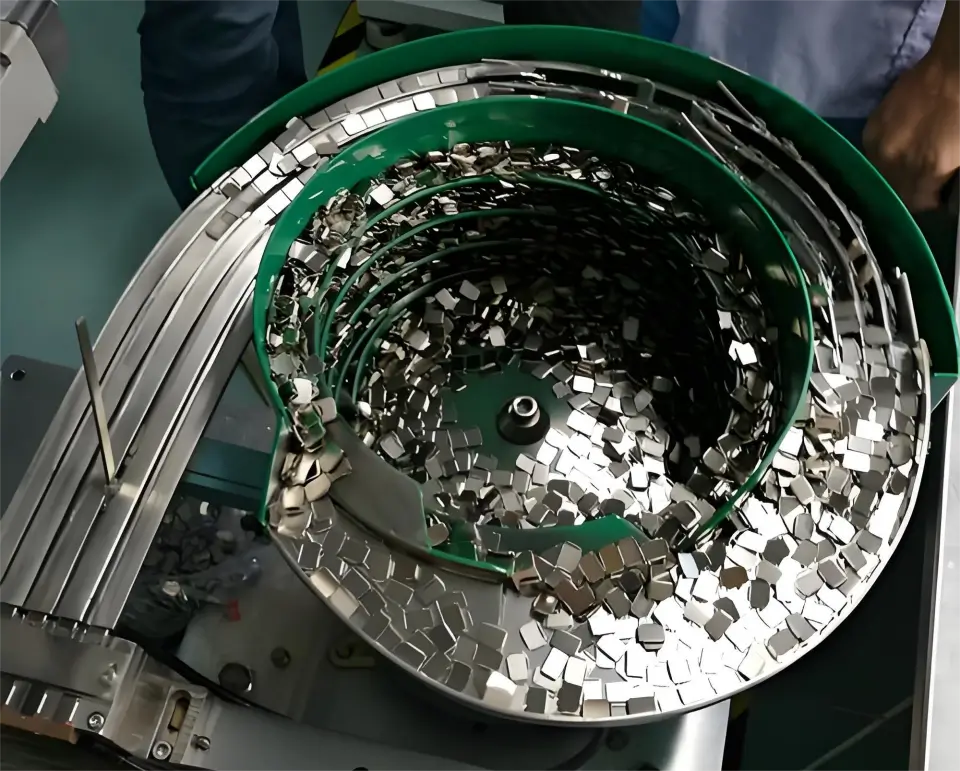
Reasons why you should choose a laser marking vision system:
- No need for jigs and fixtures: This saves you time and money, as you no longer need to create and maintain fixtures for each different type of product.
- Fast and accurate positioning: The visual positioning system can accurately identify and position your product, even if it is small or complex. This ensures that your markings are always accurate and consistent.
- Increased production capacity: The visual positioning system can automatically process multiple products at once, which can significantly increase your production capacity.
- Reduced labor costs: The visual positioning system can automate the laser marking process, which can free up your employees to focus on other tasks.
- Improved quality control: The visual positioning system can help to ensure that your markings are always accurate and consistent, which can help to reduce defects and improve product quality.
If you are looking for a reliable, versatile, and scalable marking on bulk small parts, then a visual positioning laser marking machine is a good option to consider.
What Is Laser Marking Vision System?
A laser marking vision system (also called visual positioning) is a device that uses a camera and software to automate the laser marking process. The camera takes a picture of the part for marking, and the software then identifies the desired marking location and parameters. The laser then fires at the specified location, and the marking is complete.
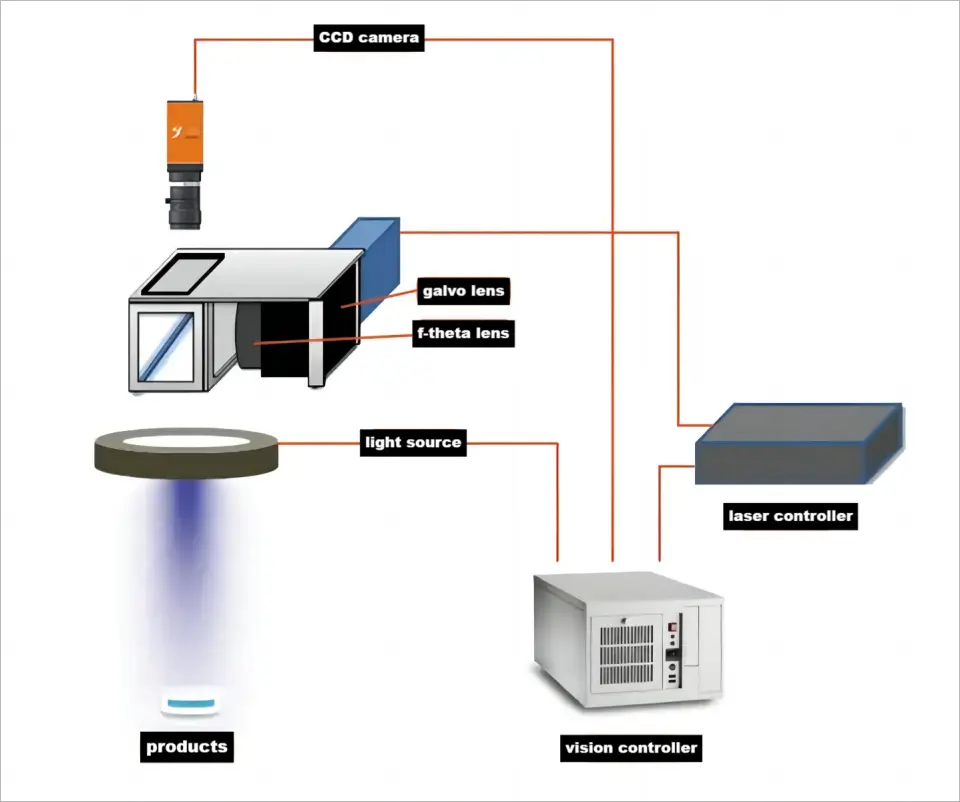
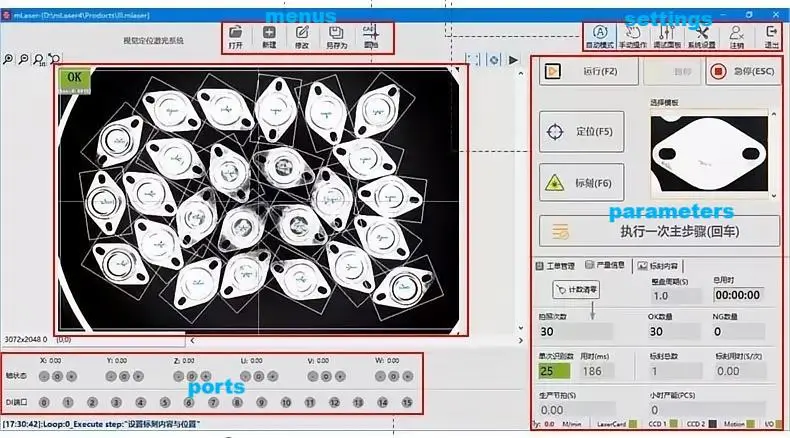
Features of Vision System:
1. Real-time image projection, fast calibration (one-step calibration), compatible with JCZ EZCAD files;
2. Accuracy: ±0.01mm (<40mm) or ±0.05mm (<100mm).
3. The product can be placed at 360 degrees, with consistent accuracy and high repeatability.
4. Powerful visual algorithm to recognize different products.
5. Compatible with conventional assembly lines on the market, realize induction marking, can control stepper, servo, AC motors, and can control double belts at the same time to improve the utilization rate of the galvanometer.
6. Support XY platform, XY module, multi-axis (6-axis) control, large-scale and large-format marking can be achieved through the slide to achieve partition segmentation marking.
7. Supports automation equipment docking, PLC docking, bar-code gun reading and MES traceability system secondary development docking.
8. Can be equipped with 6 million, 10 million, 12 million and 20 million high-resolution CCD cameras, it supports accurate marking of cylindrical and arc products such as telecentric lenses, headphones, and screwdrivers.
9. Supports visual flying marking, with a speed of up to 50 meters/min.
How Laser Marking Vision System Works?
1. Edit the marking content.
2. Adjust the marking focal length, set the marking parameters.
3. Adjust image parameters (light source brightness, contrast, exposure time), take pictures, and extract product features.
4. Import the edited marking content and place it where the product picture needs to be marked. The method of verifying the calibration accuracy: After the calibration is completed, right-click and select “Laser Marking”, the system will mark the imported graphics once at the position pointed by the mouse pointer. It is the so-called “Hit it wherever you want”, which means that the calibration data is correct, and the laser coordinates and camera pixel coordinates have been unified.
5. Carry out the visual positioning marking test, and adjust the visual capture parameters according to the actual situation (including similarity, pattern angle, etc.)
Laser marking vision systems are applicable in a variety of industries, including small hardware, tools, phone parts, watches, electronics, and medical parts.
Different work tables for option when we use vision system for marking:
- Fixed worktable, suitable for feeding the workpiece manually
- Transfer belt with go-stop mode, suitable for multiple products at one-time marking
- Transfer belt with sensor, suitable for one product one marking
- X-Y sliding table, suitable for disk shape product marking
- Flying mode, suitable for high speed non-stop marking
Here is a video of how the laser marking vision system works:
Share this post